Customized Centrifuge Options
Because Not All Sludge is the Same
Our Open-Minded Approach to Decanter Centrifuge Design Creates a Best-In-Class Solution for Sludge Dewatering and Thickening
Centrisys is not a “one-size-fits-all“ type of centrifuge manufacturer. We go further with customized centrifuge design options to meet or exceed the requirements of each job. Our company size allows us to react quickly. Our 30+ years of focused centrifuge experience allows us to leverage what we know from our portfolio of municipal and industrial dewatering and thickening installations. We pride ourselves on being a strategic partner, not just a centrifuge supplier. We don’t believe you should change your process requirements to meet a standard centrifuge design. We’ll work with you to find the right equipment, should it be standard, semi-standard or a fully customized decanter centrifuge.
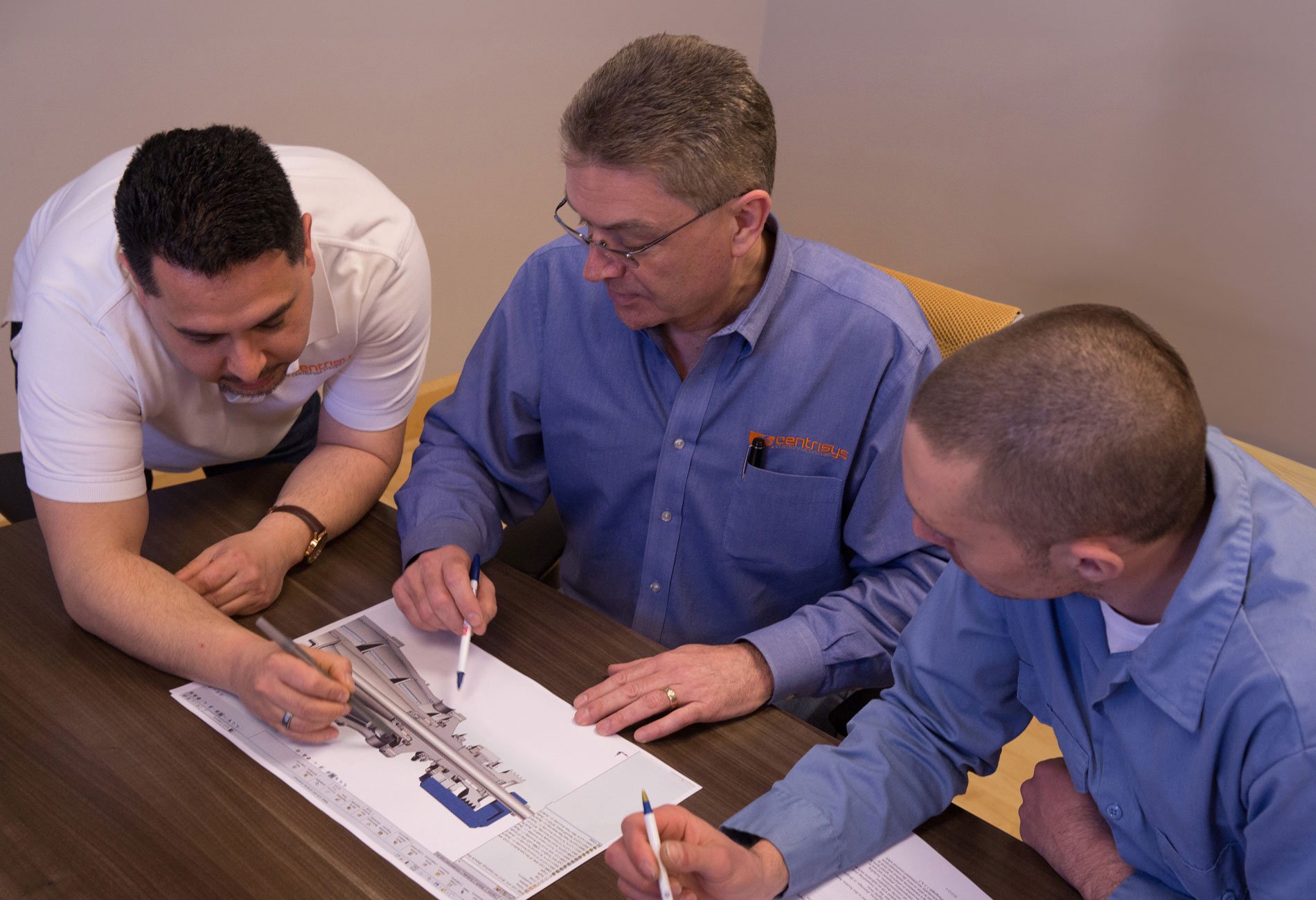
We Don't Stand Still. Our Centrifuge Customization Process is Continuous.
2-Phase Decanter Centrifuges for Dewatering Sludge & Slurries
A decanter centrifuge, also known as a solid bowl centrifuge continuously separates solids from a liquid with high solids concentration. The centrifuge bowls high speed of rotation (G-force) causes the solids to deposit onto the bowl wall. The built-in screw conveyor (scroll) moves in the same direction as the bowl, but slightly slower and continuously transports the solids to the conical end of the bowl, where drying occurs before the solids are discharges from the centrifuge. The clarified liquid (centrate) is then almost completely free of the solids and exits through openings at the opposite end of the bowl.
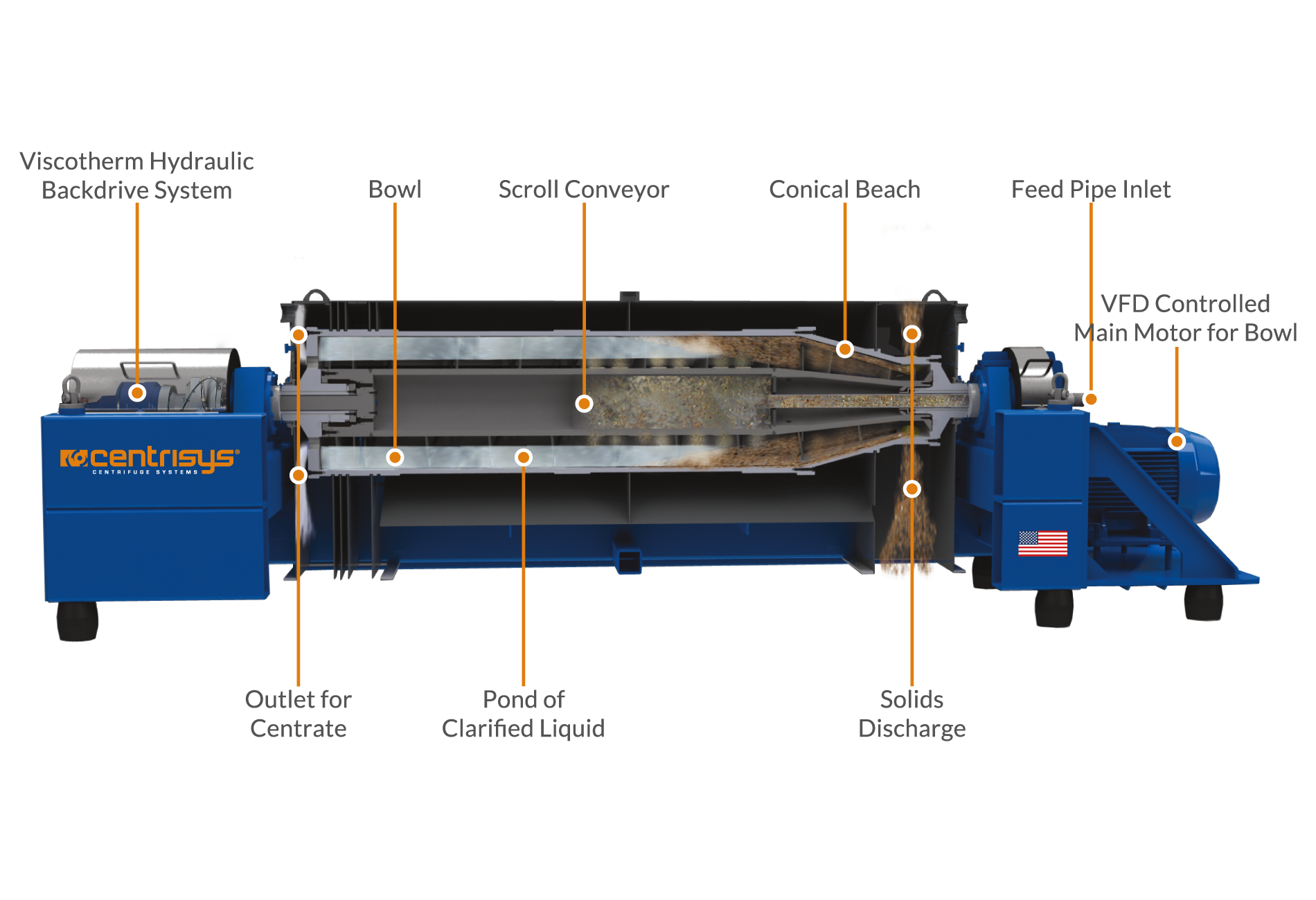
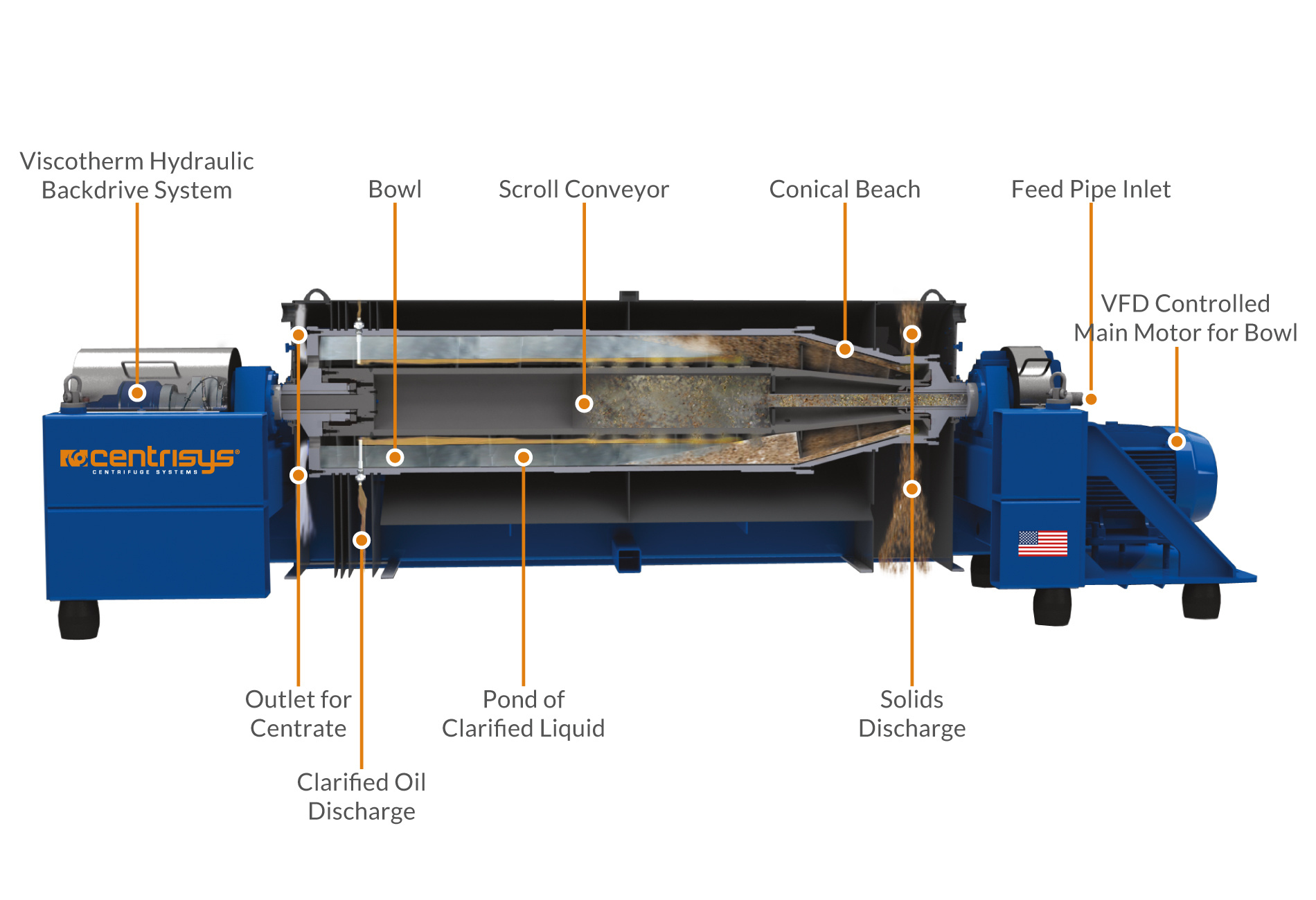
3-Phase Decanter Centrifuges
Clarifies and simultaneously separates two liquids of different densities from a solid. The bowl's high speed of rotation causes the solids to deposit on the bowl wall while the built-in screw conveyor continuously transport the solids to the conical end of the bowl where further drying occurs prior to being discharges from the centrifuge. The separated liquid phases are then almost completely free of solids and exit through separate openings at the opposite end of the bowl.
Design Solutions to Tackle a New Process or Optimize an Older Centrifuge
Our customized solutions can be as large as designing and building a complete mobile dewatering or thickening trailer or as small as improving a wear part. Our RD, engineering, manufacturing and service teams bring value to the development process by being involved at virtually every stage— from concept through design and prototyping to production and end-of-life support.
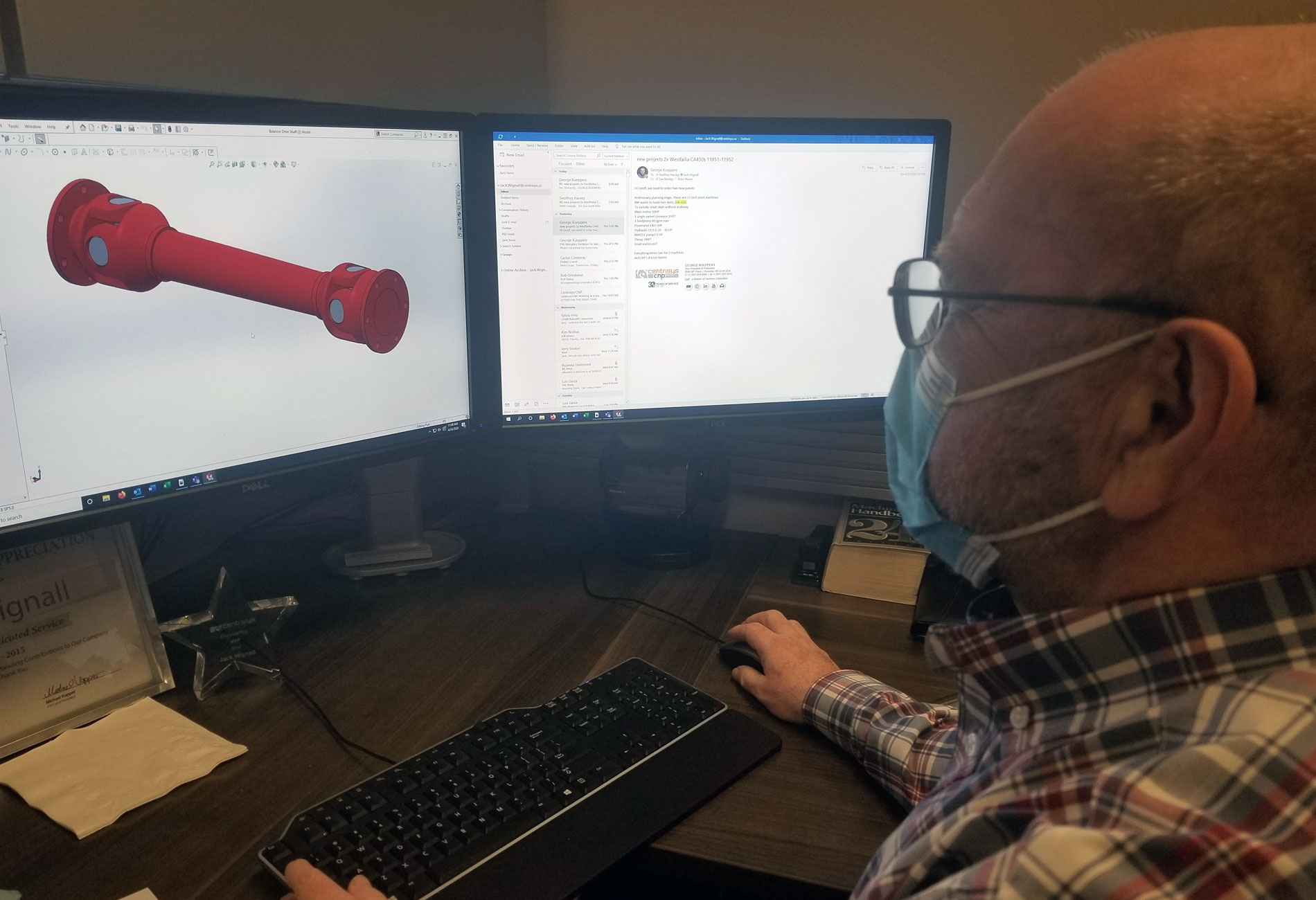
"We knew we needed to optimize older, traditional coal industry centrifuge technology but didn't know how. Our goal was to have a coal product with consistent moisture between 15-23% which has not been done in the industry. It's been through our partnership with Centrisys, first through their extensive knowledge of not only centrifuges but the process of dewatering, then thru lab analysis, concept, prototype, pilot testing and optimization that we have developed a best in class coal recovery and dewatering process."