Features & Benefits
9 Reasons to Choose Centrisys
1. U.S.A. Engineering and Design
Built from the Ground Up
By way of passionate drive and ambitious character, Michael Kopper began a mission to create the most efficient decanter centrifuge in the industry. In 1987, the first Centrisys centrifuge was designed and built around what was learned in the field by servicing competitor’s equipment in both municipal and industrial applications.

Thirty years later, the Centrisys engineering team continues to benefit from problem-solving and learning what does and does not works in the real world. They take that knowledge and continue Centrisys’ lifelong commitment to brand excellence. A Centrisys centrifuge is designed, engineered and built with pride at our corporate headquarters in Kenosha, Wisconsin.
2. Highest Quality
A Standard, Not an Option
- All structural rotor components are centrifugally cast* or forged for ultimate integrity and strength.
- Centrifugally cast bowls are made of A890 duplex stainless steel, offering substantially higher tensile strength and greater corrosion resistance compared to 316SS.
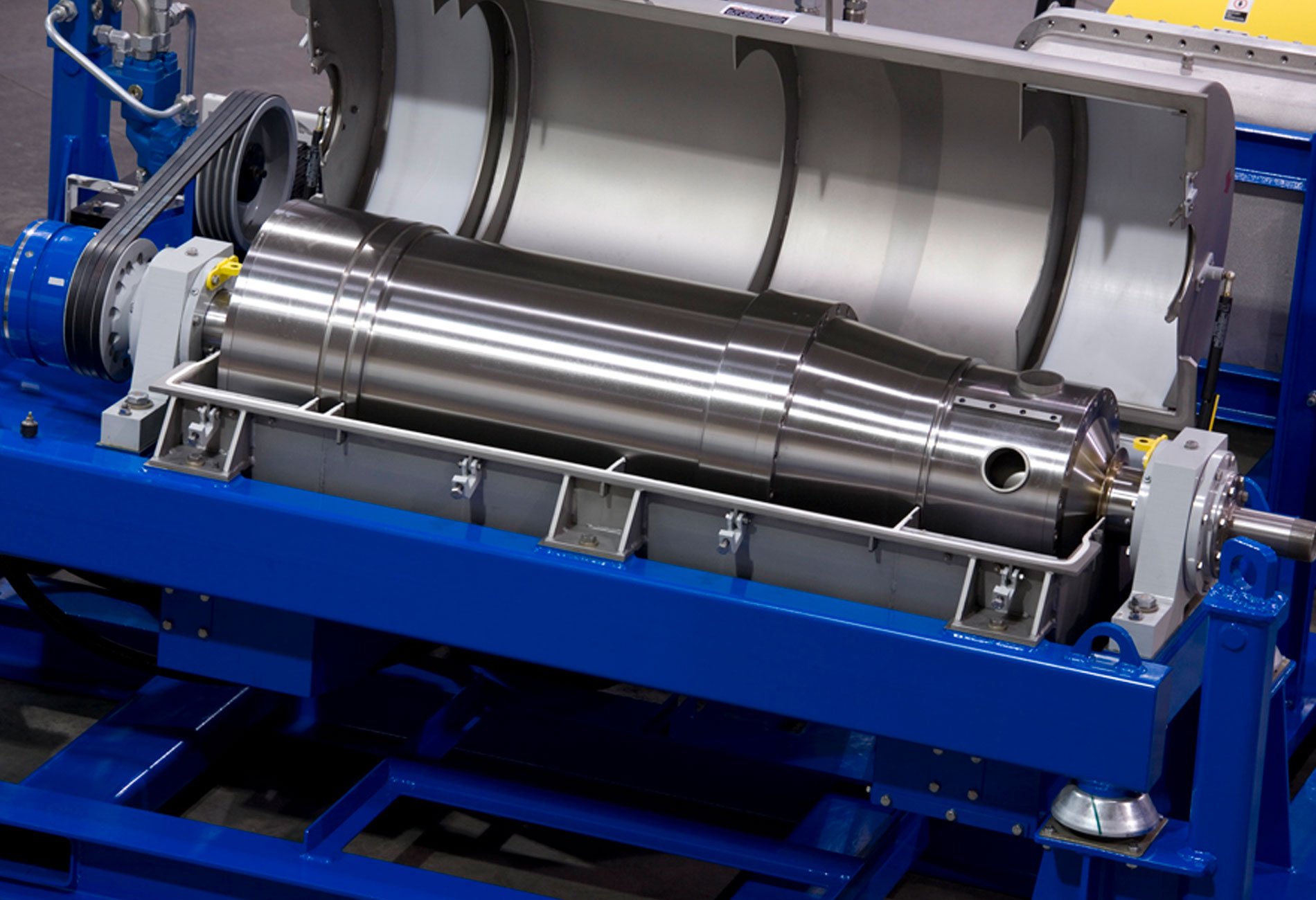
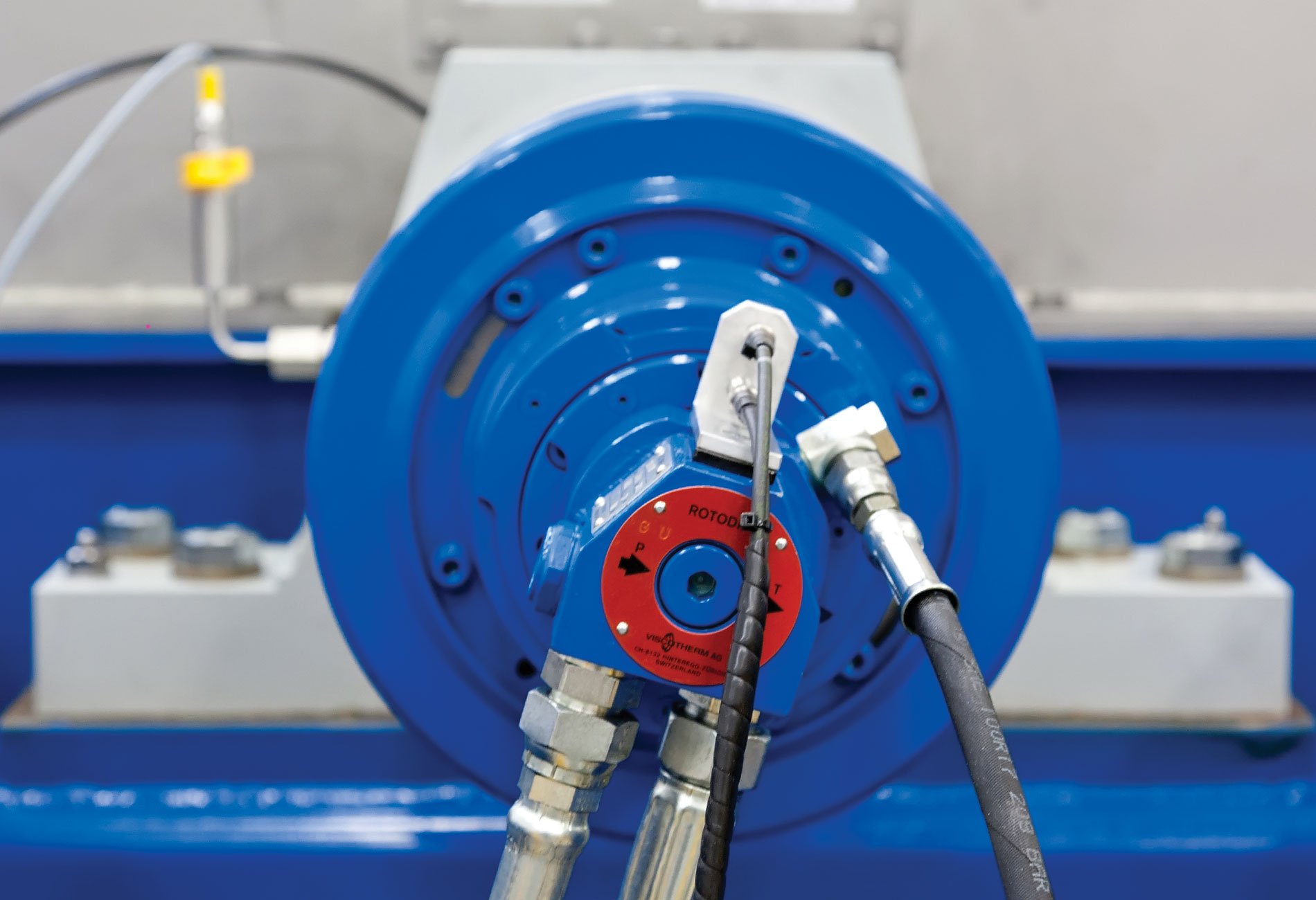
3. Automatic Hydraulic Scroll Drive
Most Efficient Backdrive in the Industry
- Highest torque to weight ratio.
- 100% torque at all speeds (including standstill).
- Low weight.
- Reliable/durable.
- Increased solids loading capacity.
- Low energy consumption (power is not lost or wasted).
- Versatile design for multiple applications.
- Simple and accurate measurement of scroll speed.
- Lowest overhanging load – lighter weight equals less stress on the main bearings.
Refer to the Centrisys Hydraulic Scroll Drive Brochure to review advantages of a hydraulic back drive vs. the gearbox design.
4. Advanced Wear Protection
Standard on all Centrisys Centrifuges
Why is this important? It prolongs the life of the centrifuge, increases uptime, optimizes performance and reduces service and maintenance costs.
- Scroll flight tips in a high solids area are protected with replaceable tungsten carbide tiles and offer the highest wear protection possible.
- Feed acceleration nozzles are made of replaceable tungsten carbide offering the highest degree of toughness.
- Bowl is protected by longitudinal wear strips allowing the solids layer to anchor between the strips and provides optimal protection from wear on the bowl.
- Tungsten carbide replaceable cake discharge nozzles minimize repair and/or replacement.
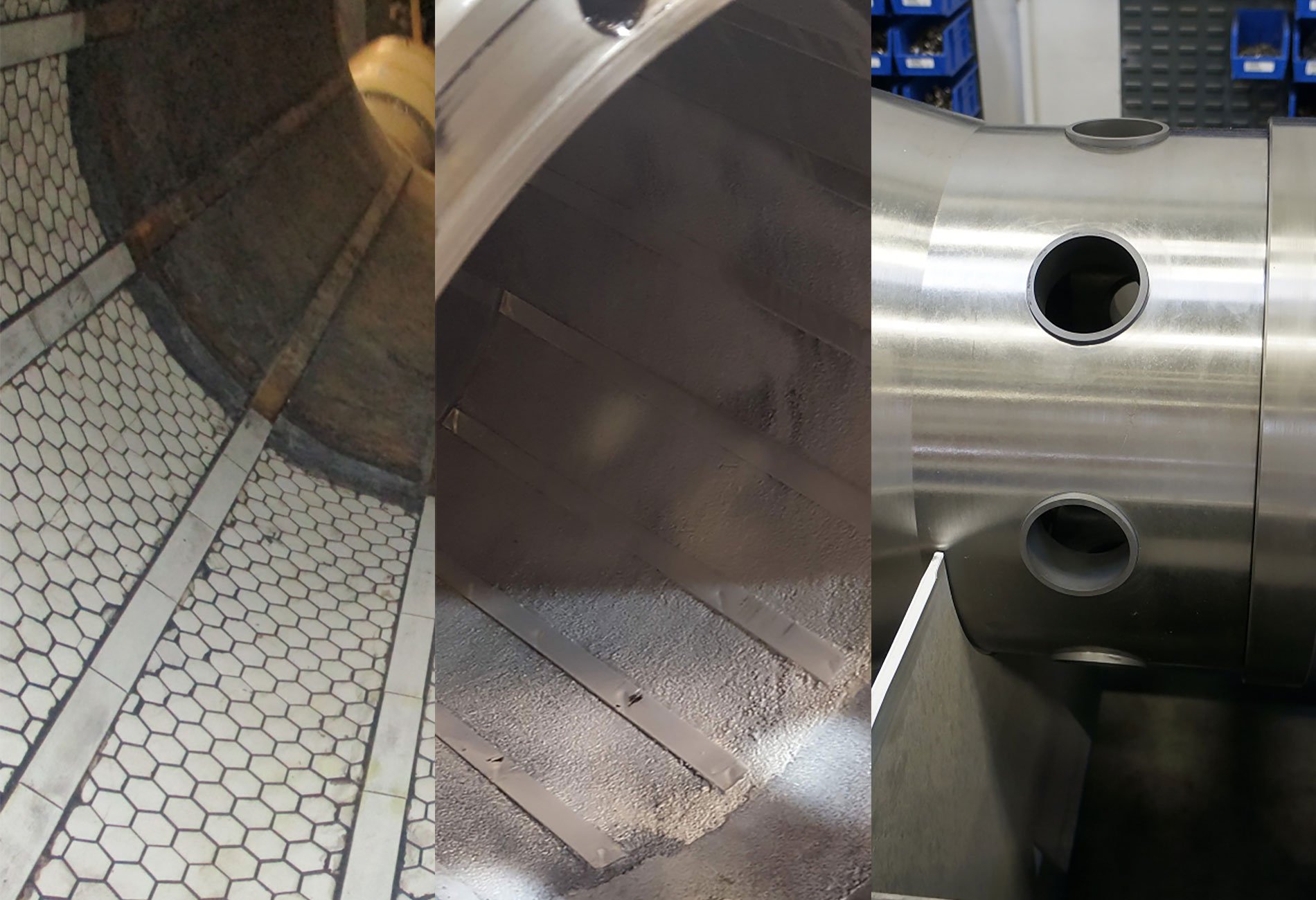
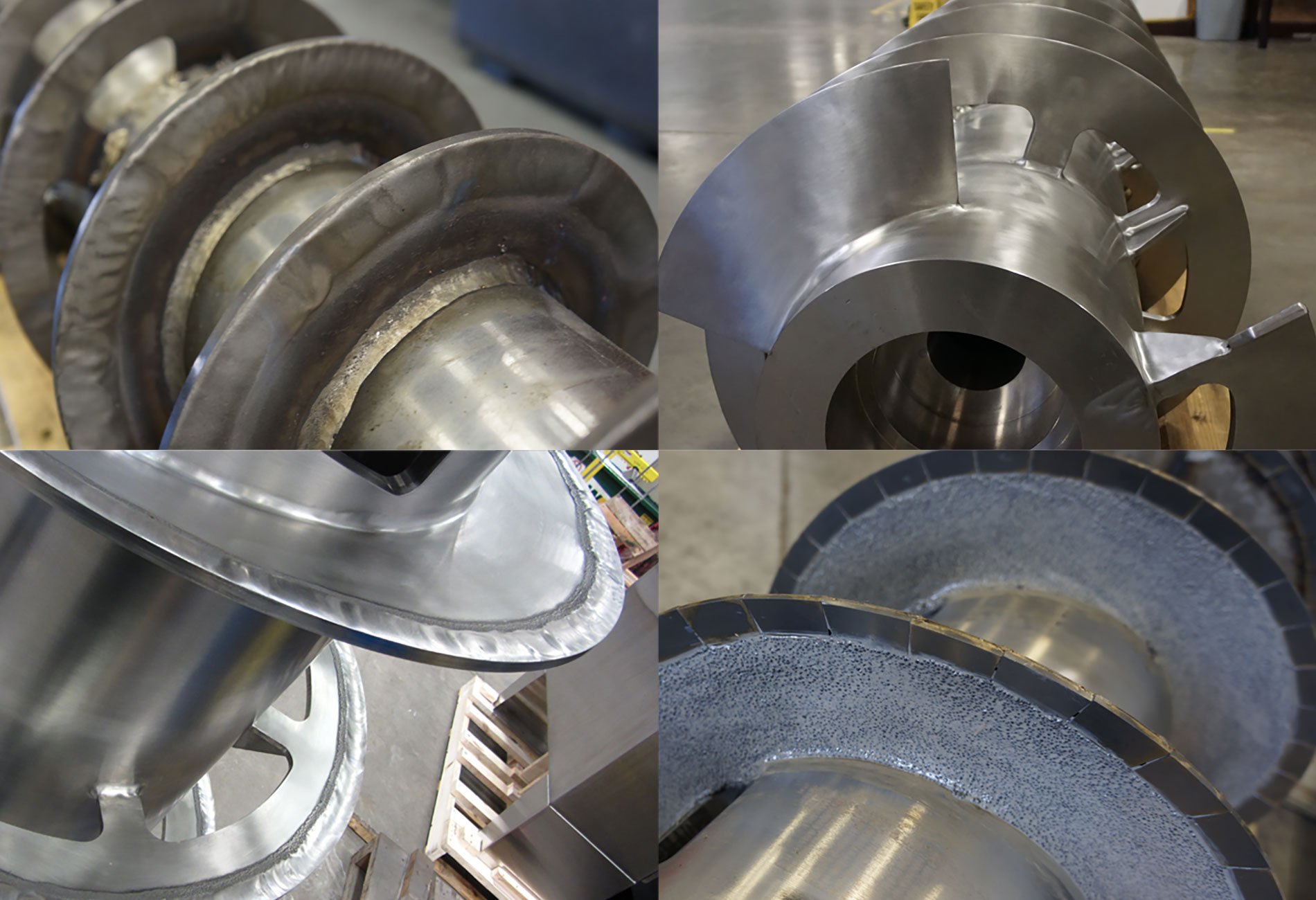
5. Scroll Design and Development
- Ultra-deep pool with a narrow scroll body.
- Removes dewatered solids at a controlled rate to preserve equilibrium and maintain solids balance.
- Incorporates an axial flow design, which promotes settling of even the finest solids, improves the recovery rate and reduces polymer consumption.
- High flow design = larger and more feed ports, allowing for efficient and gentle acceleration of the treated sludge.
- Leading and lagging rotational scroll optimizes performance and increases the time frame needed between service.
6. Optimum Beach Angle*
Two machines with the same length and diameter, but with different beach angles, offer different capacities.
- A shallow beach has a longer cylinder, creating more clarification volume.
- A steeper beach gives greater capacity provided all solids can convey up the beach while maintaining a high bowl speed and G forces.
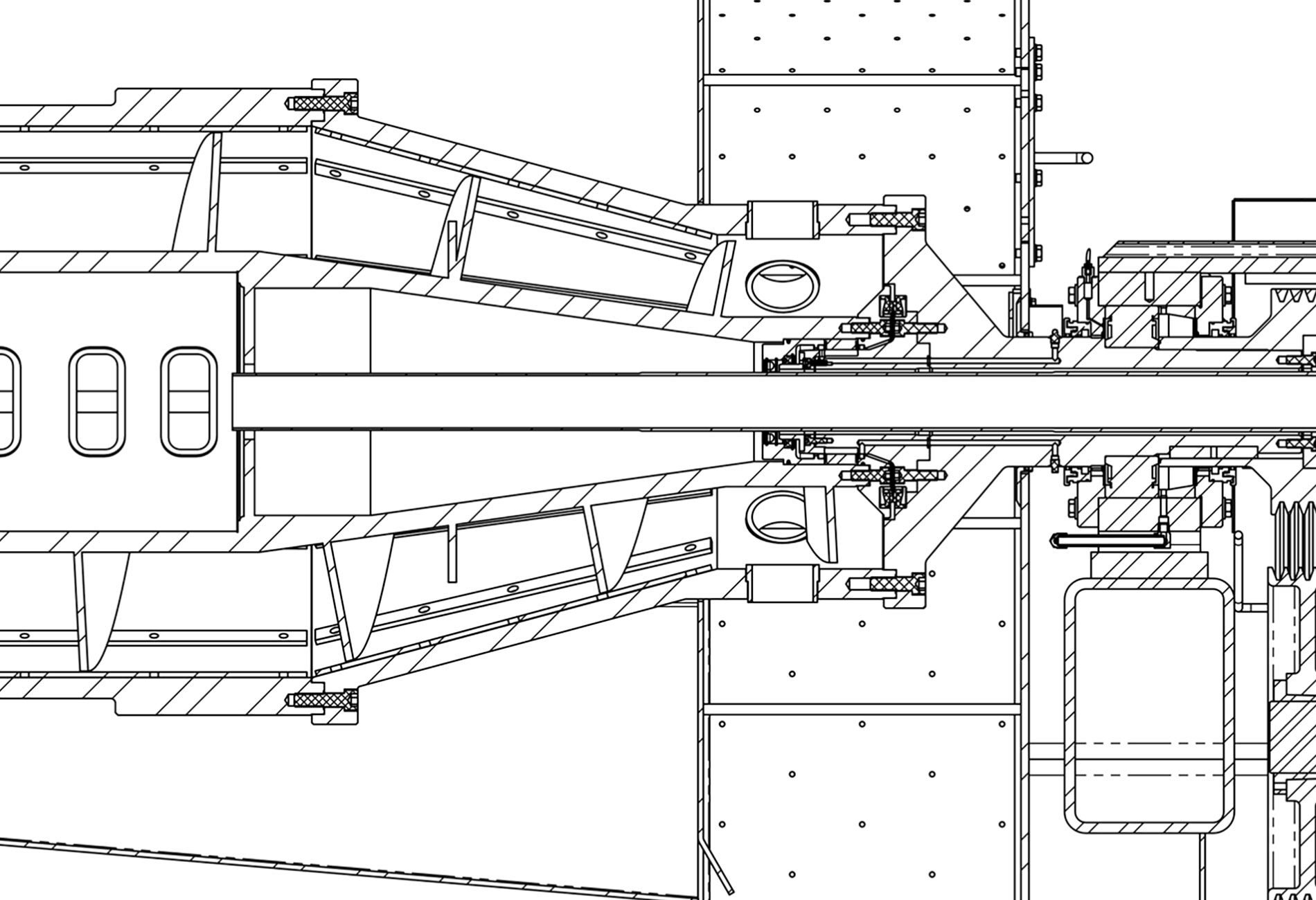
Over the years, Centrisys tested various bowl angles from 8-90 degrees and established that a 15 degree angle is optimum for typical municipal wastewater applications. A mineral or mining dewatering process require a shallow beach angle of 8-10 degrees.
*The Centrisys engineering teams consult with customers, conduct field and lab testing as well as analyze performance data to determine the optimal beach and L/D ratio for each application.
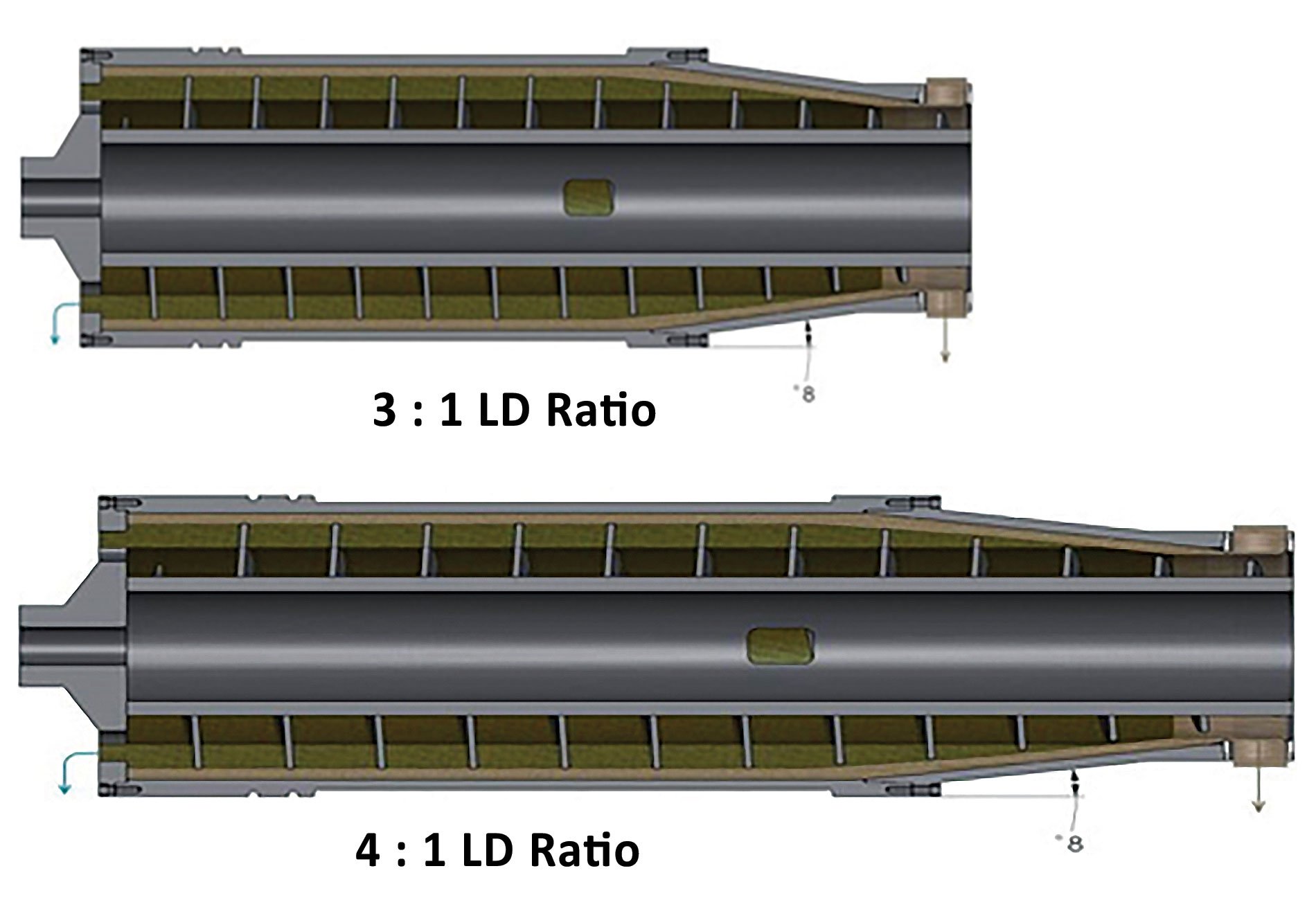
7. L/D Ratio*
The “L/D ratio” is the overall internal bowl length divided by the bowl inside diameter in the cylinder.
- Machines that have a smaller L/D ratio are better suited for processes that have high specific gravity solids that settle well.
- Machines with higher L/D ratios are better suited for lighter solids that need more time to settle from the liquid phase.
*The Centrisys engineering teams consult with customers, conduct field and lab testing as well as analyze performance data to determine the optimal beach and L/D ratio for each application.
8. Centrifuge Energy Recovery System (CERS)
CERS is a self-contained system using variable frequency drives on both the main drive motor and the backdrive. The drives function independently, under normal circumstances, and support each other in the case of a power outage. During a power outage, the centrifuge continues to empty preventing a costly dis-mantle to free-up a blockage. If power returns during shutdown, the centrifuge can re-start on the fly. Benefits include:
- Reduced main drive and backdrive horsepower, up to 25% reduction.
- Increased reliability and on-line process time, +10 points.
- Improved handling of power disruptions.
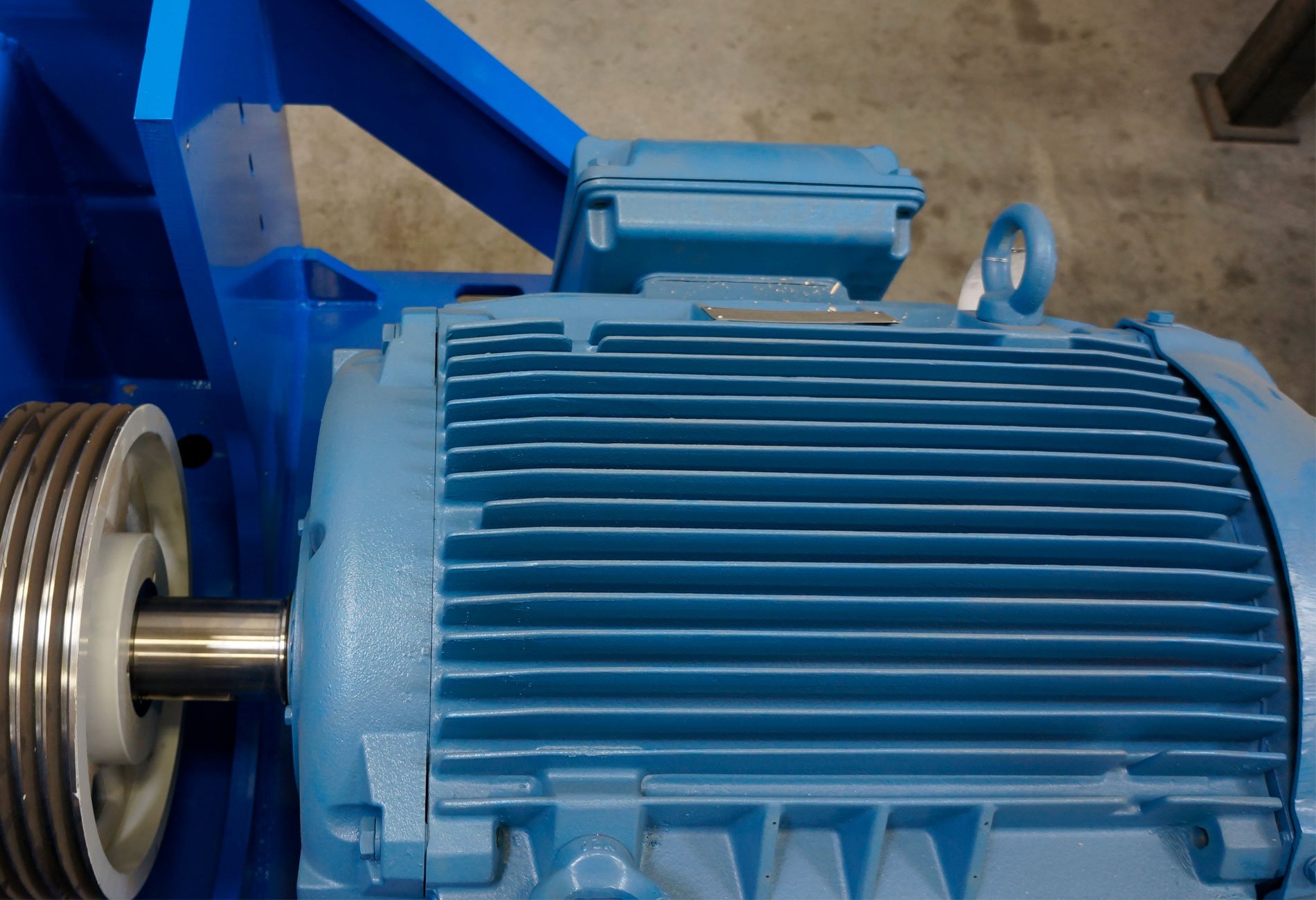
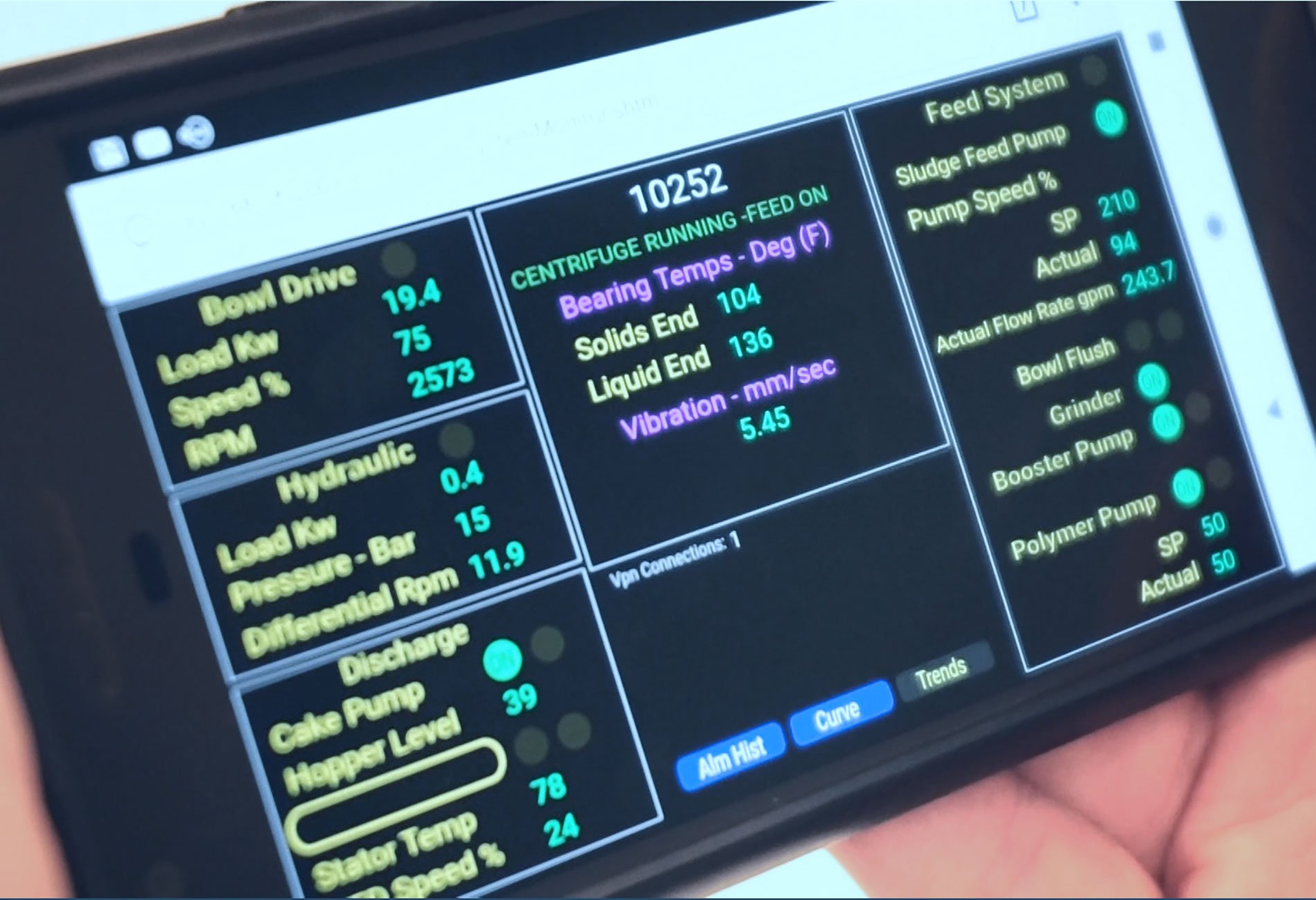
9. Remote Monitoring System
The Centrisys Remote Monitoring System is a proprietary remote solution. It provides 24/7, real-time text and email alerts for equipment status changes and process variations within the system. The system provides timely insights to ensure peak performance, the highest reliability and lowest operating costs.
Contact Us to Learn More About Centrisys/CNP's Capabilities
We're dedicated to providing innovative solutions that enhance the efficiency and effectiveness of your processes. Whether you're looking to optimize performance, reduce operational costs, or explore our industry-leading technology, our team is here to help.
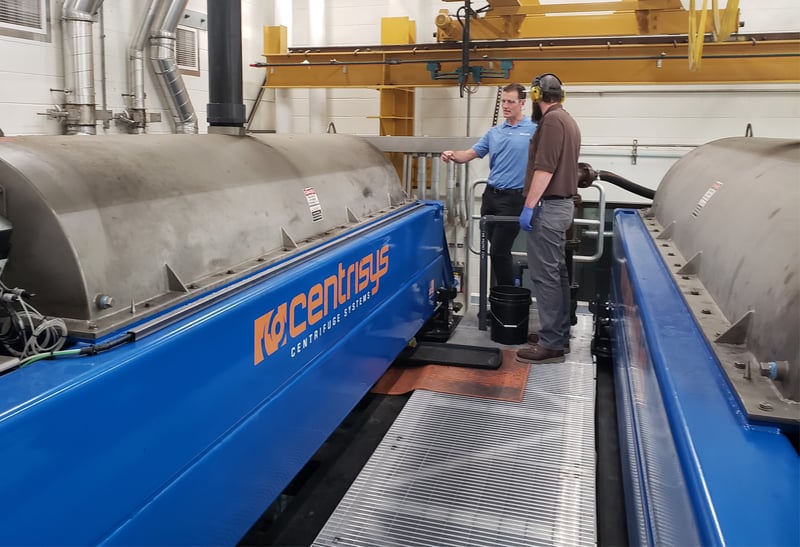