Is Your WWTP Spending Too Much Money on Ferric to Meet Phosphorus Regulations?
Q&A with Gerhard Forstner, President of CNP
Download Your Guide NowTable of Contents
- What is struvite and what is struvite’s impact on municipal or industrial water treatment facilities?
- What are the main benefits of MagPrex?
- How can a plant manage the recovered struvite?
- Are there risks associated with not implementing a nutrient recovery program?
- Why should your plant choose Centrisys/CNP for your next sludge treatment and nutrient recovery project?
- What are the cost considerations for installing MagPrex as your nutrient recovery process?
- Is MagPrex the only technology Centrisys/CNP has to aid in advanced biosolids treatment?
- What is the best way to predict MagPrex performance at a plant?
MagPrex: Struvite Removal for Municipal and Industrial Applications
MagPrex™ is a nutrient recovery process owned by Centrisys/CNP. MagPrex, a flexible solution for nine to 220 MGD plants, installs between the anaerobic digester and dewatering equipment. The process forms struvite by using the soluble orthophosphate and ammonium present in the sludge. Using aeration, MagPrex strips out the CO2 to increase the pH and adds magnesium chloride (MgCl 2) to augment the magnesium (Mg2+). The struvite crystallizes and settles on the bottom of the reactor tanks.
To understand MagPrex better, Gerhard Forstner, President of CNP, answers engineers' questions.
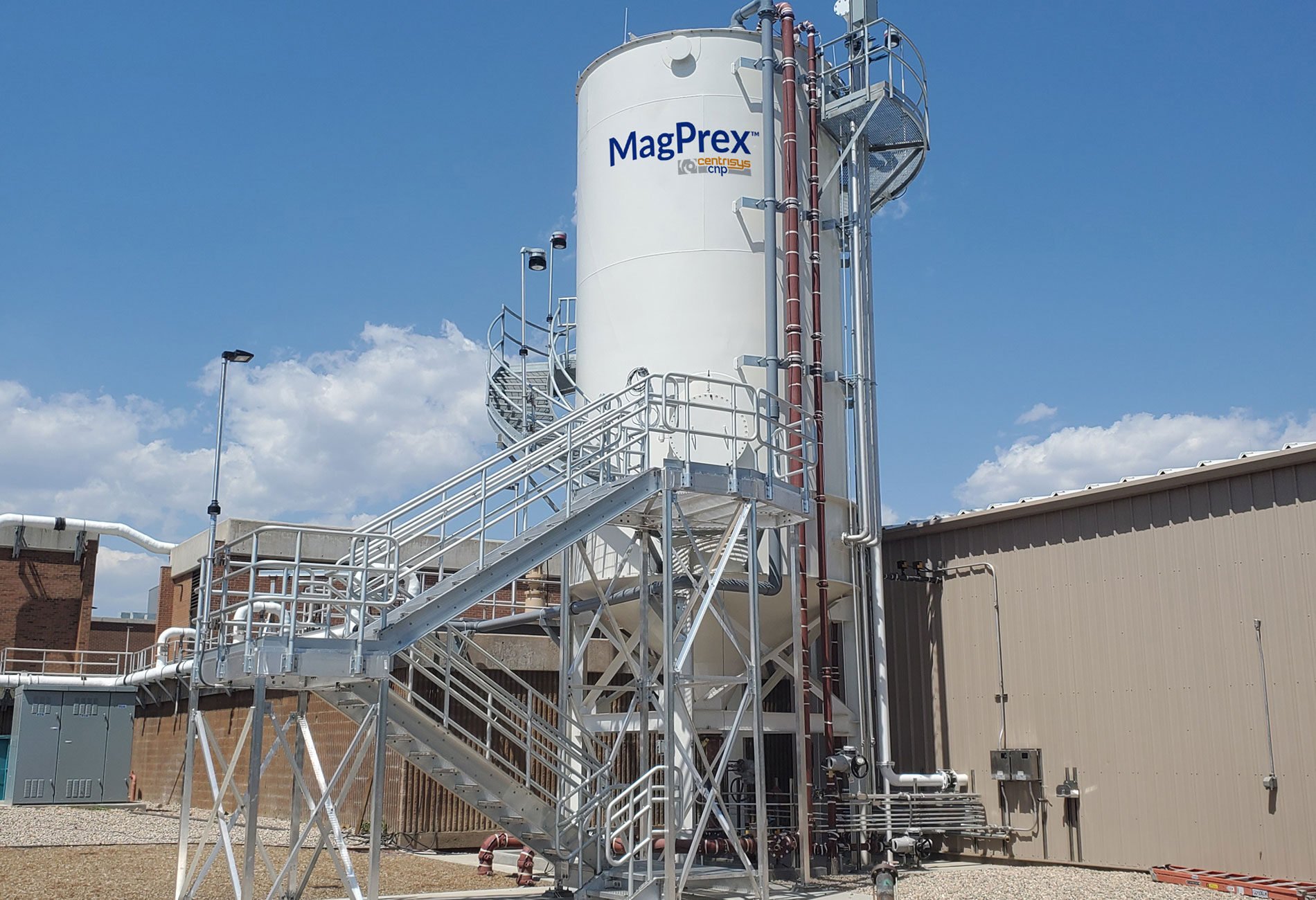
Struvite (NH₄MgPO₄·6H₂O) is a mineral consisting of magnesium, ammonium and phosphorus which are common molecular compounds found in municipal and industrial wastewaters. These compounds are found in higher concentrations in the anaerobic digestion phase of the solids handling side of wastewater management and combine to form struvite under neutral pH conditions. Struvite scaling forms on rough surfaces. This causes struvite clogged pipes in pumping equipment, digesters and other wastewater processes. Struvite increases maintenance time and maintenance costs at a plant.
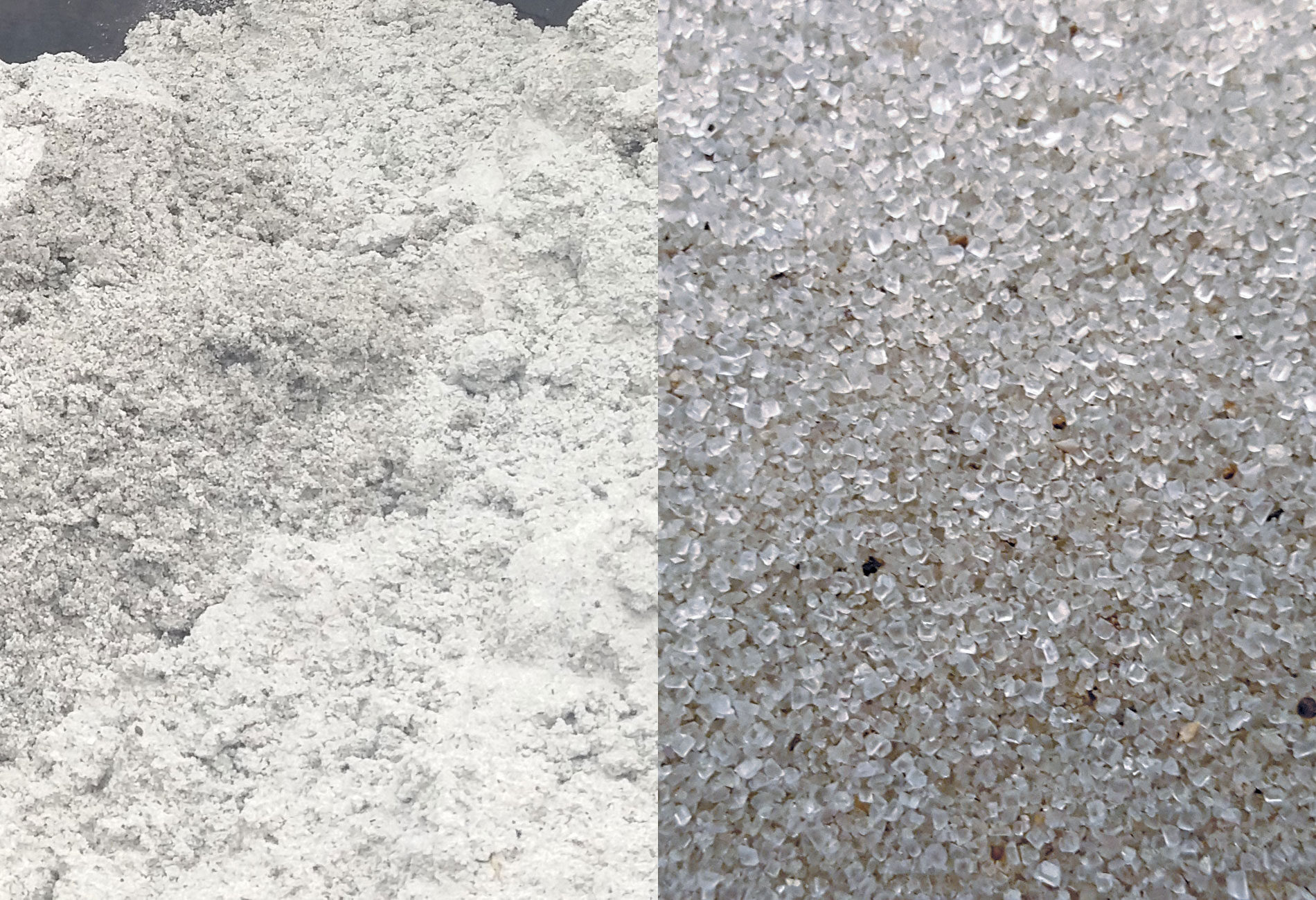
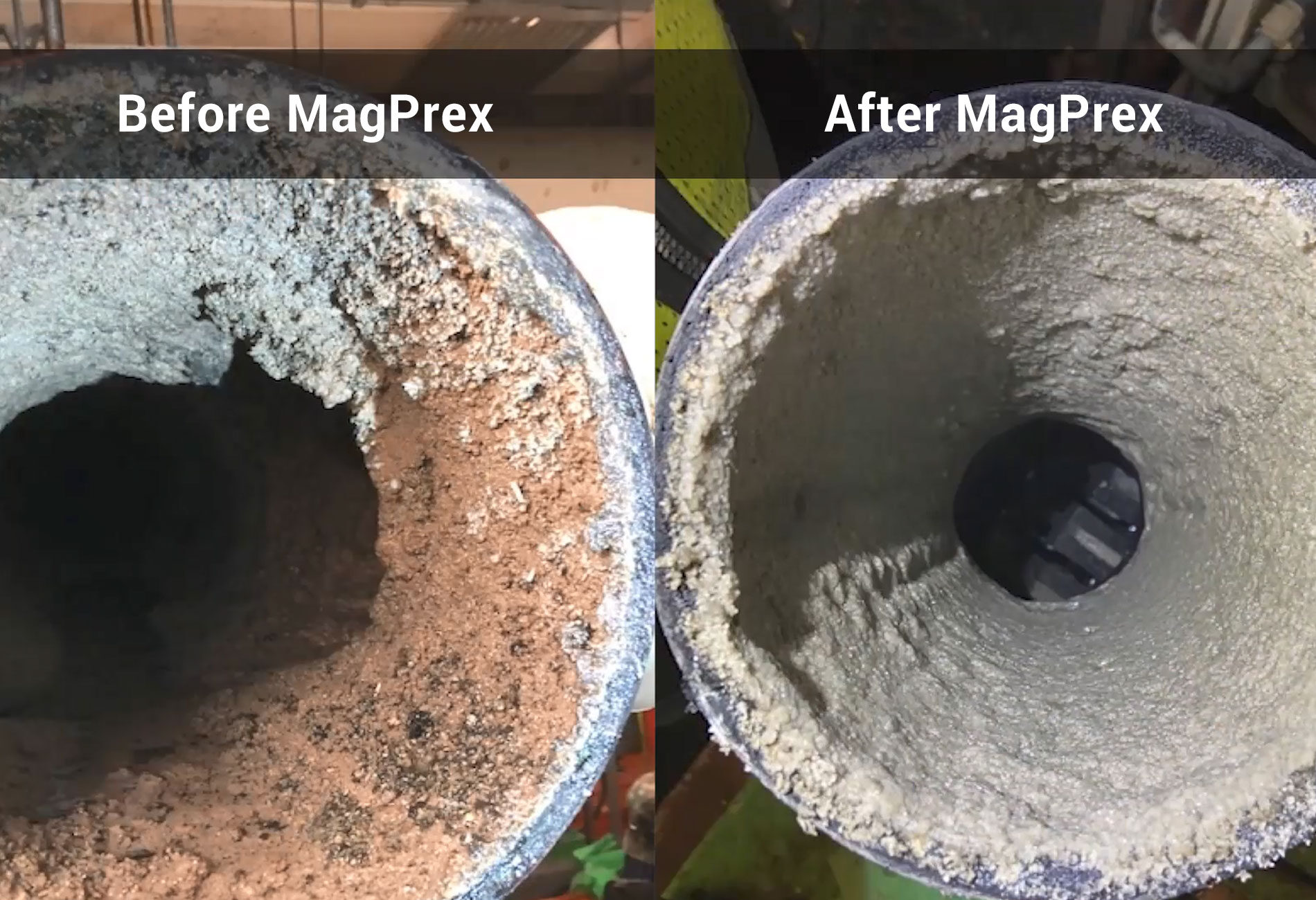
What are the main benefits of MagPrex?
There are several benefits associated with the MagPrex nutrient recovery process. MagPrex installations achieve a 90% or greater reduction in soluble orthophosphate in the return sidestream from the dewatering process which goes back to the head of the plant. This reduces the overall plant phosphorus concentrations, including effluent discharge, to surface waters. MagPrex process also increases dewatered cake dryness up to 3% higher percent total solids (%TS) and reduces polymer use 20-30% to achieve current %TS dryness, which helps optimize the sludge treatment process. MagPrex reduces maintenance costs associated with uncontrolled struvite formation in downstream systems. By reducing the available orthophosphate in the waste stream, struvite is less likely to form and makes downstream piping easier to maintain.
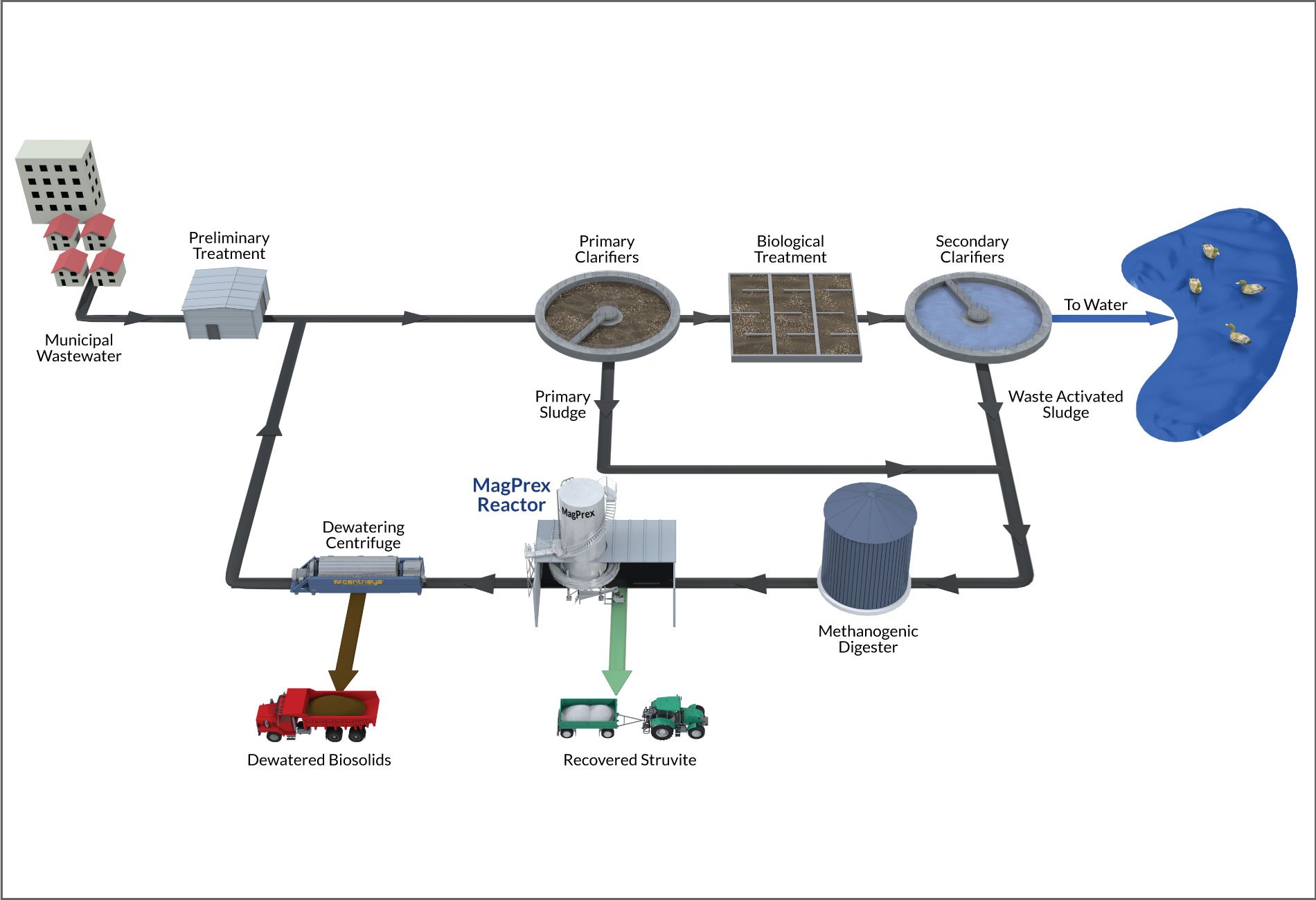
INSTALLATION UPDATE:
Drake Water Reclamation Facility | Fort Collins, Colorado
The water reclamation facility has achieved very low effluent phosphorus limits, below 0.5 mg/L. The MagPrex reactor reliably removes more than 90% of orthophosphate from the phosphorus recycle loop going back to the front of the plant. That allows the Drake Water Reclamation Facility to consistently meet the lower phosphorus discharge limits set by the Colorado Department of Public Health & Environment (CDPHE). Watch the Fort Collins case study to learn more.
INSTALLATION UPDATE:
Central Valley Water Reclamation Facility | Salt Lake City, Utah
MagPrex phosphorus removal is currently making its way through engineering submittals. Project specifications include >85% orthophosphate removal and future struvite harvesting capabilities. This installation also includes five Centrisys THK350 sludge thickeners for primary and WAS sludge.
Yes, there are risks for a plant not using a nutrient recovery program. Concentrated orthophosphate in the centrate stream from the dewatering phase is often recycled back to the headworks of the treatment facility. This causes a feedback loop and an accumulation of orthophosphate concentrations in the solids handling stream over time. High orthophosphate levels cause severe maintenance issues such as struvite pipe scaling, digester scaling, centrifuge scaling or scaling in other plant equipment. Higher soluble orthophosphate reduces centrifuge dewatering performance by requiring more polymer and decreasing the biosolids cake %TS.
MagPrex helps break the feedback loop by converting the available soluble orthophosphate and ammonium in the anaerobically digested solids stream into struvite before it can form in downstream processes. The orthophosphate concentrations are reduced greatly in the return centrate stream. The plant achieves lower nutrient discharge concentrations in the effluent, provides improved centrifuge dewatering performance and reduces preventative maintenance from struvite scaling. If your plant does not implement a nutrient recovery program, future lower TP effluent limits and regulations may not be met.
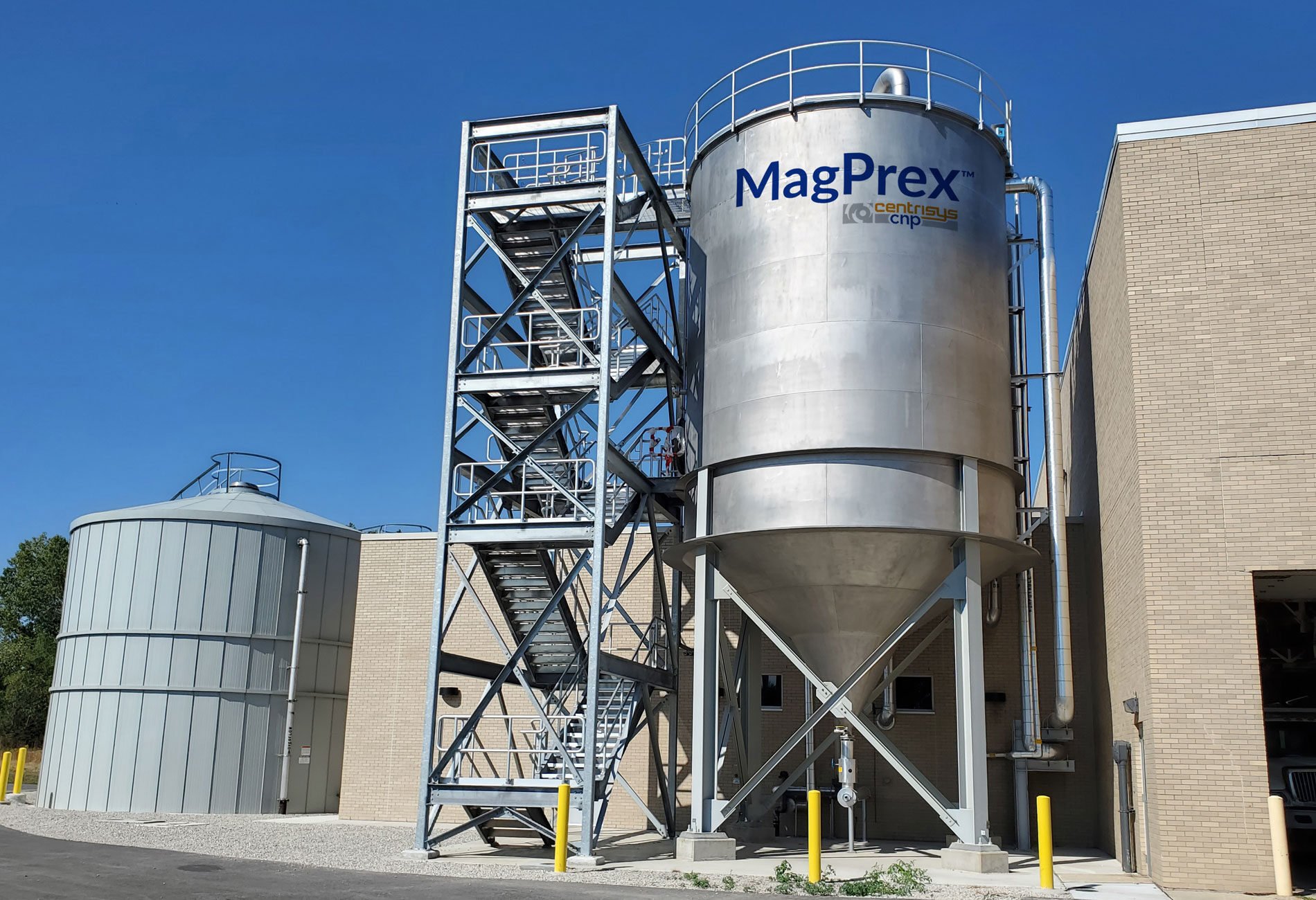
INSTALLATION UPDATE:
Fox River Water Reclamation District | Elgin, Illinois
The district installed MagPrex to process anaerobically digested sludge and sequester soluble phosphorus as struvite. MagPrex is currently being optimized but has already recorded effluent soluble phosphorus concentrations of less than 25 mg/L. By reducing the soluble phosphorus, MagPrex decreases the struvite build-up maintenance costs and the flow efficiency loss for downstream treatment processes such as dewatering.
It is very important to work with a company like Centrisys/CNP because we are the only company that understands both sludge treatment and nutrient recovery. Centrisys has over 30 years of sludge dewatering experience. We manufacture decanter centrifuges and sludge thickeners. In 2014, we partnered with CNP to add nutrient recovery to our portfolio and have dedicated project managers and engineers that understand the nutrient process.
Today, we have five full-scale MagPrex systems installed throughout the USA and three more currently under construction. A majority of the MagPrex projects are paired with Centrisys dewatering centrifuges.
INSTALLATION UPDATE:
Metro Water Recovery | Denver, Colorado
This is a 220 MGD facility and is the world’s largest struvite recovery installation from digestate. The plant paired MapPrex with eight Centrisys CS26-4 decanter centrifuges and has an annual $600,000 dewatering and disposal cost savings.
Watch the Denver case study to learn more.
There are several cost benefits associated with the MagPrex process. MagPrex uses a 30% solution of MgCl2. Magnesium chloride is competitively priced compared to ferric or polyaluminum chloride (PAC) and is an easier chemical to handle. MagPrex also improves the dewatering stream cost analysis. The solids hauling costs are decreased since there is a higher %TS. This results in polymer savings since the polymer dosage amount is decreased. Also, by decreasing the soluble phosphorus in the return stream, MagPrex reduces the maintenance required on downstream processes. This includes the digesters since the overall phosphorus load is reduced back into the treatment stream.
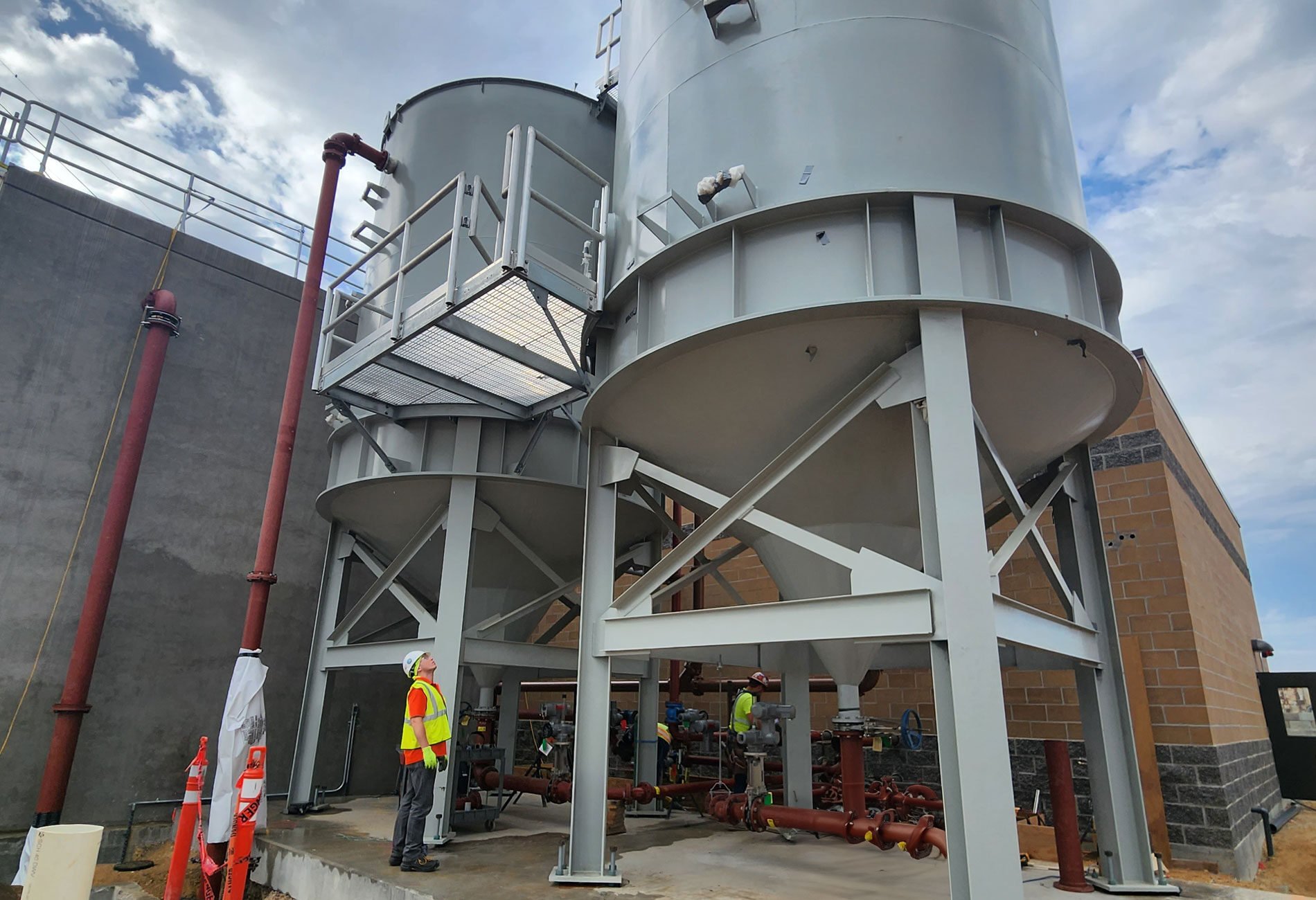
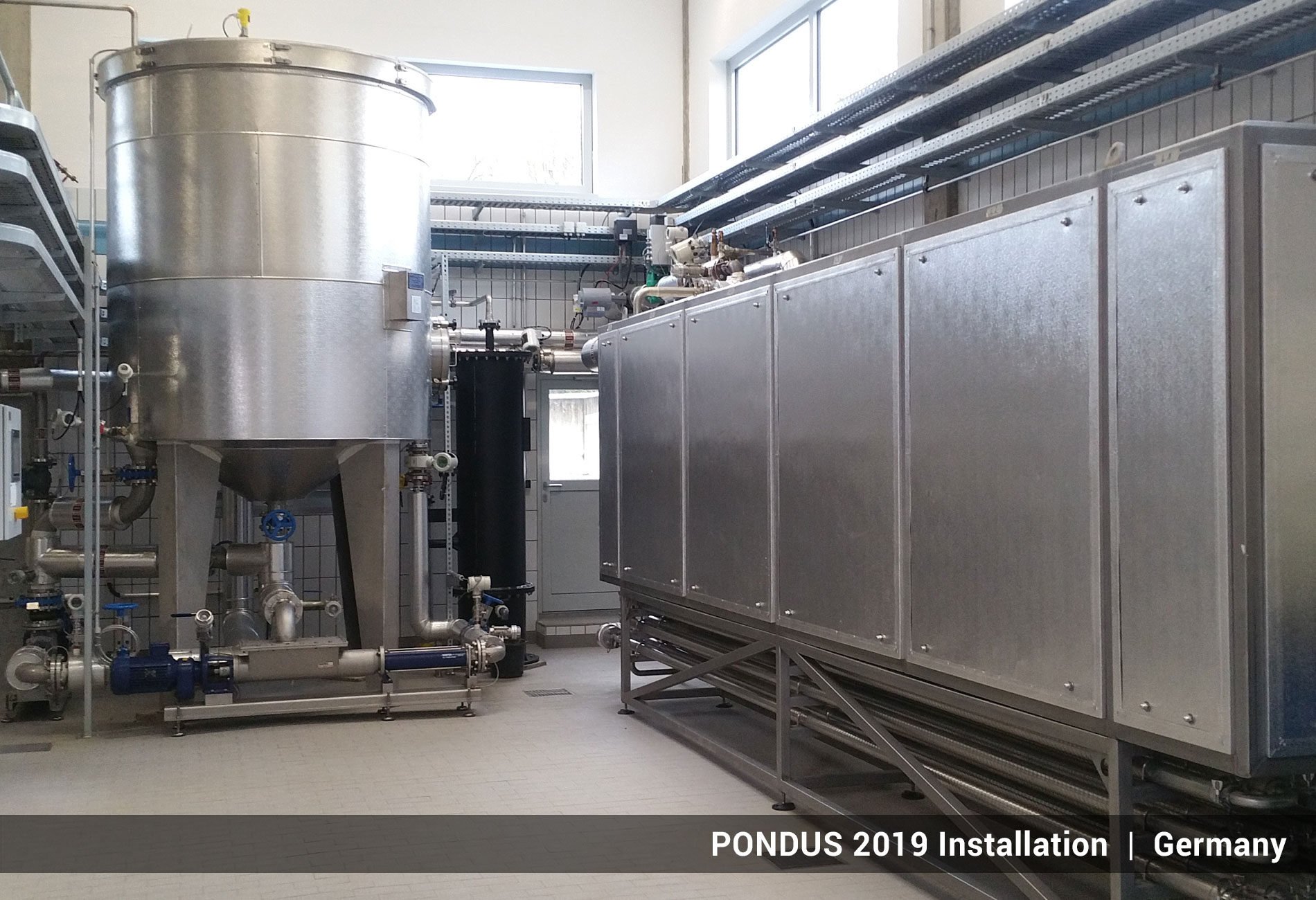
CalPrex is a pre-digestion technology that recovers phosphorus as a brushite crystal with up to 41% P2O5 (phosphorus pentoxide) and can minimize digester and sidestream phosphorus loading by over 50%. PONDUS is a thermal hydrolysis process (THP) that uses low-grade heat (140 °F to 160 °F) and sodium hydroxide. PONDUS does not require a pressure vessel, reduces biosolids disposal costs up to 30% and improves digester performance.
Some MagPrex results can be conducted in the lab. Centrisys/CNP can arrange feasibility testing with sludge provided by the plant. This testing confirms available soluble orthophosphate for the MagPrex process and estimates the expected chemical dosage for a full scale installation. For more accurate results, a MagPrex pilot unit is available to conduct on-site testing.
Contact us today if you have questions or want to find out more about how MagPrex can benefit your plant. By requesting a sample analysis or pilot test, our knowledgeable team can perform either an on-site or off-site sample analysis.
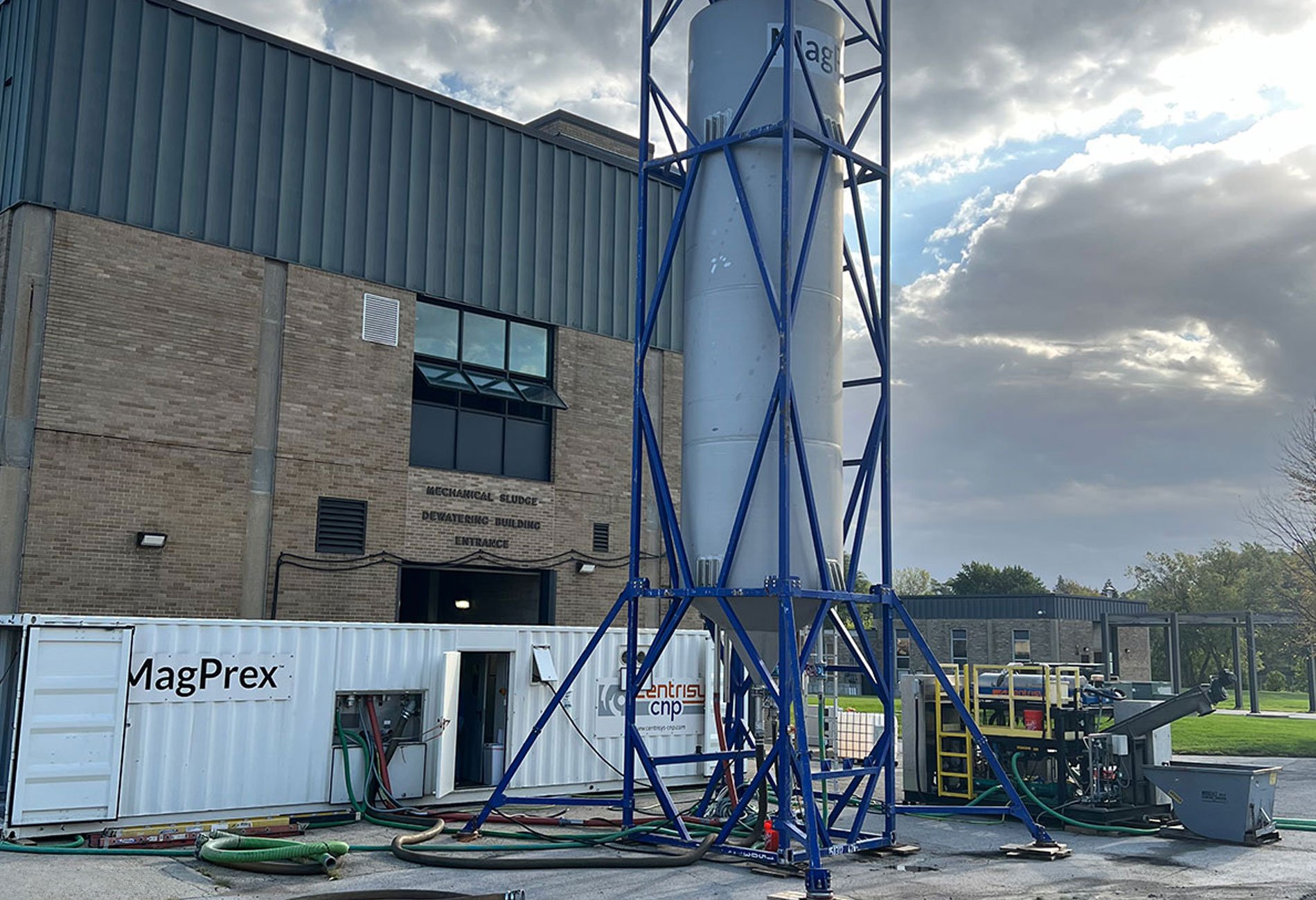