Decanter Centrifuge Repair | Rebuild | Remanufacture
Centrifuge Repair Services
Decanter Centrifuge Repair
Urgent Centrifuge Repair Response, Because You Can't Afford to Wait
We’re here when you need us most. We provide repair, rebuild, fabrication and remanufacturing services for all makes, models and brands of decanter centrifuges. We understand dewatering applications are not all the same, and it’s our job to make sure you always get the most out of your separation equipment.
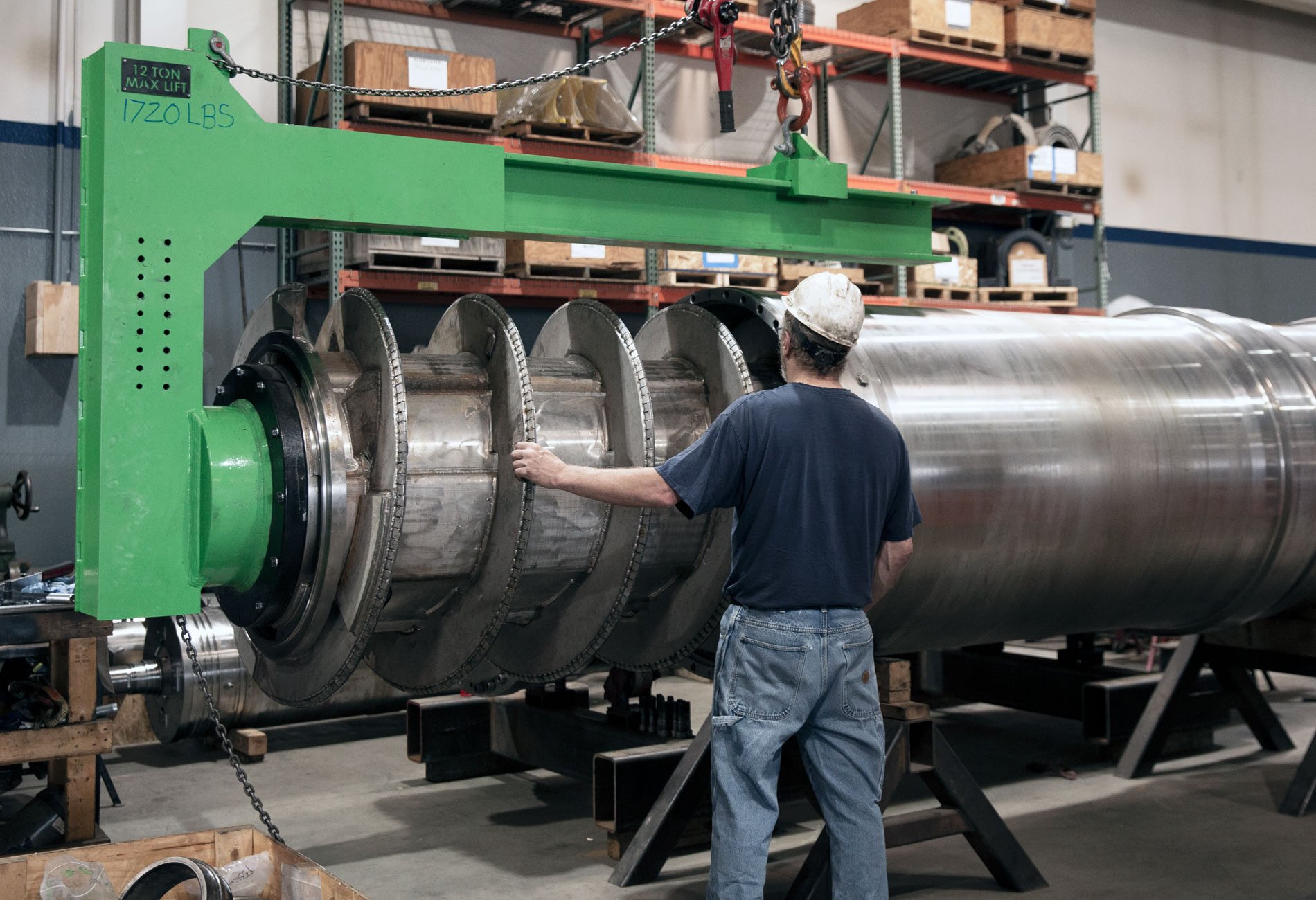
- Measuring all critical fits and dimensions and comparing each decanter centrifuge to OEM standards before we start
- Sizing and evaluating all centrifuge wear components and scrolls to original standards
- Analyzing centrifuge and parts wear points, friction and stress factors
- Using 3D software modeling and FEA (Finite Element Analysis) to design and improve existing parts and maximize performance
- Rotating assembly and scroll exchange programs allow for the quickest turnaround possible
Centrifuge Repair Services
- Decanter Centrifuge Repair Services including:
- Centrifuge rebuild
- Centrifuge repair
- Centrifuge remanufacturing
- Centrifuge fabrication
- Centrifuge reconditioning
- Upgrades and retrofit
- Preventative maintenance
- Process evaluations/optimization
- Installation assistance
- Centrifuge Inspection Services
- Vibration analysis and other diagnostic services
- Operator and maintenance training
- Maintenance agreements
- Flight repair and replacement
- High speed dynamic balancing
- Control Panel Automation and upgrades
- ISO 9001:2015
Our repair services are available 24 hours a day, 7 days a week. We have centrifuge repair locations throughout the US, Canada and worldwide. Contact us to schedule a repair or receive an estimate.
Decanter Centrifuge Bearing Repair and Diagnosis
In this 3-minute video, learn how to diagnose internal and external bearing damage on a decanter centrifuge.
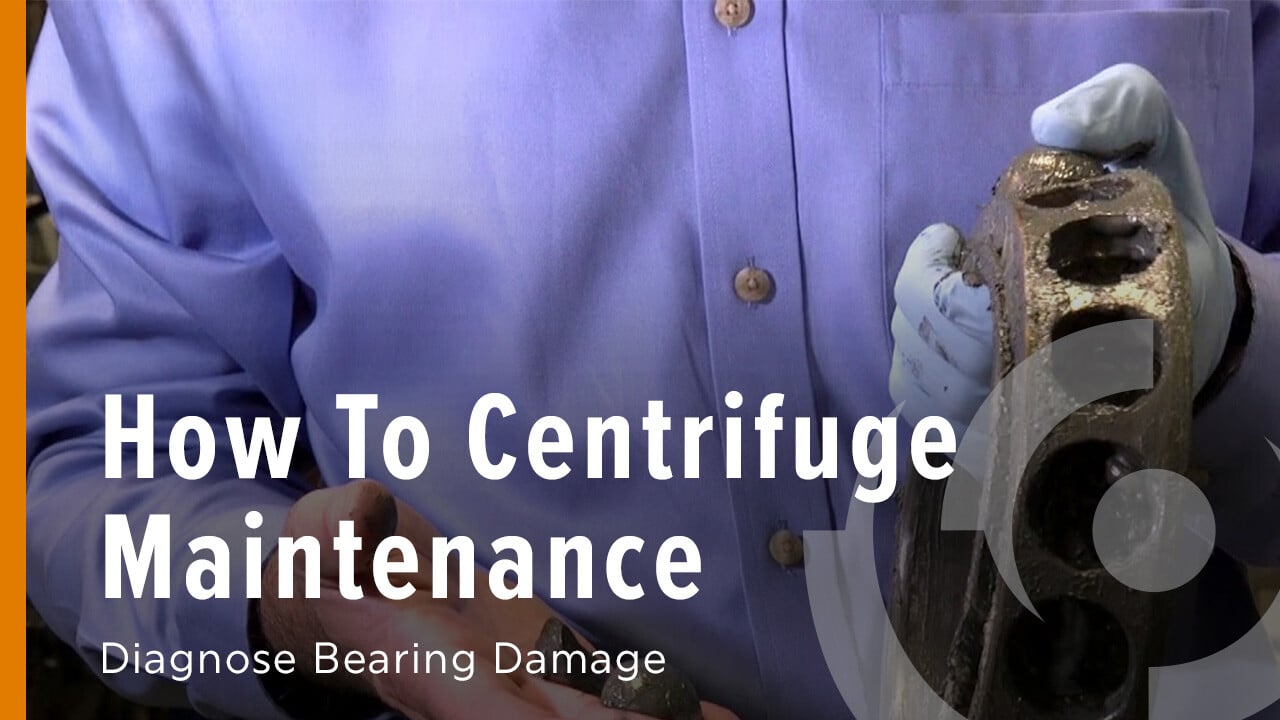
We Invest in Our Commitment to Advanced Centrifuge Repair Equipment
We use:
- Dynamic, high-speed, hard bearing balancers
- Horizontal boring mills for scroll, bearing housing and frame repair
- Plasma cutters for scroll fabrication and repair
- Manual and CNC lathes
- Manual engine lathes
- Dust ventilation for removing harmful fumes and particles for our welders
We also continue to expand our capabilities through:
- In-stock centrifuge parts for all brands of decanter centrifuges
- New, high-end manufacturing equipment
- Hiring and training additional service technicians and machinists for factory and on-site service
- More repair locations – currently in: Kenosha, Wisconsin; Stockton, California; Houston, Texas; Germany; Spain; Chengdu, China; Singapore; Brazil; Argentina
Literature
- CSI: A 40+ Point Centrifuge Inspection Program
- Direct Replacement for 3-Stage Planetary Gearbox on the Derrick 7200 Centrifuge
- Decanter Centrifuge Parts Available When You Need Them
- Urgent Centrifuge Repair Response, Because You Can't Afford to Wait
- Enhance Performance and Extend the Life of your Decanter Centrifuge
Videos
Need an Urgent Repair? Contact Centrisys/CNP
Service That Never Stops — Nationwide and Global. Centrisys/CNP is always ready to repair, maintain, and optimize any decanter centrifuge make, model, or brand. Our expert technicians are available 24/7, wherever you are. Don’t wait — contact us now for urgent repairs.
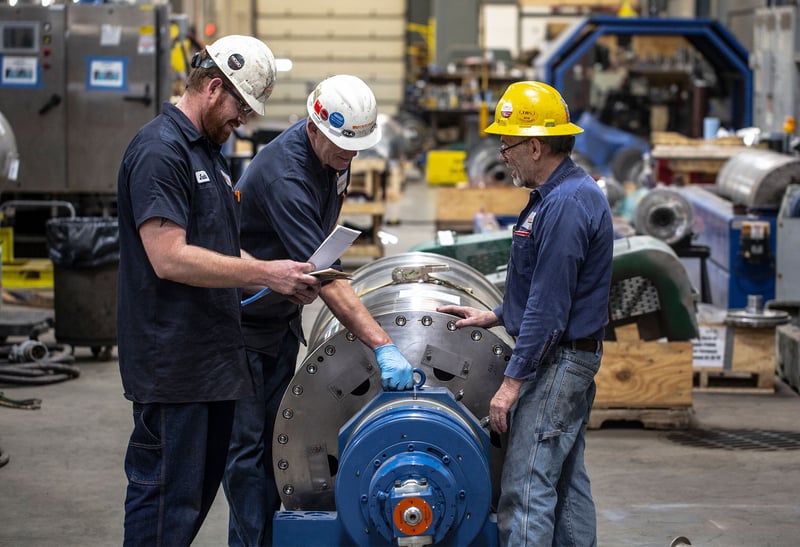